Product Knowledge
Equipment Configuration of 800TPH Artificial Sand Making Plant
author:dahua2 time:2025-03-14
The 800tph artificial sand making plant is an efficient and complex production process. It requires a series of professional equipment to work together to ensure the stable operation and efficient output of the production line. The following is a detailed introduction to the key equipment that makes up this production line.
Feeding system
The feeding system is the starting link of the sand and gravel aggregate production line, responsible for feeding the raw materials into the crusher evenly and continuously. For the 800-ton-per-hour production line, large vibrating feeders such as GZD series or ZSW series vibrating feeders are usually selected. These equipments have the characteristics of simple structure, stable operation, and uniform feeding, which can ensure that the raw materials enter the crusher at an appropriate speed and flow rate, thereby improving the crushing efficiency.
Crushing system
The crushing system is the core part of the sand and gravel aggregate production line, which is responsible for crushing the raw materials into the required particle size. According to the hardness and particle size distribution of the raw materials, the crushing system is usually divided into three stages: coarse crushing, medium crushing and fine crushing.
1. Coarse crushing equipment: The coarse crushing stage mainly uses jaw crushers, such as PE1200*1500 jaw crushers. The jaw crusher has the characteristics of simple structure, reliable operation, and large crushing ratio. It can quickly crush large pieces of raw materials into smaller particles, preparing for the subsequent medium and fine crushing stages.
2. Medium crushing equipment: In the medium crushing stage, cone crusher or impact crusher can be selected according to the hardness of the raw materials. Cone crusher is suitable for crushing high-hardness raw materials, such as river pebbles, basalt, etc., and has the characteristics of reliable operation, high output, and uniform particle size. Impact crusher is suitable for crushing medium-hard raw materials, such as limestone, and has the characteristics of large crushing ratio, fine products, and good particle shape.
3. Fine crushing equipment: Sand making machine or impact crusher, such as VSI series sand making machine, is usually used in the fine crushing stage. These equipment can further crush the raw materials after medium crushing into the required particle size, while ensuring the particle shape and particle size distribution of the product.
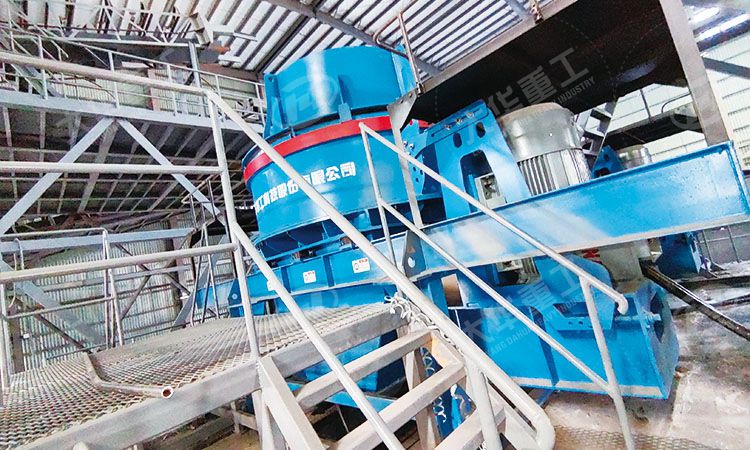
Conveying system
The conveying system is responsible for transporting the crushed materials from one device to another to ensure the continuous operation of the production line. Commonly used conveying equipment include belt conveyors and plate conveyors. Belt conveyors have the characteristics of simple structure, stable operation, and long conveying distance, and are suitable for long-distance and large conveying volume occasions. Plate conveyors are suitable for short-distance and small conveying volume occasions, and have the characteristics of compact structure and reliable operation.
Screening system
The screening system is responsible for screening the crushed materials to separate products of different particle sizes. Commonly used screening equipment includes circular vibrating screens and linear vibrating screens. Circular vibrating screens have the characteristics of simple structure, high screening efficiency, and large processing capacity, and are suitable for screening large-particle materials. Linear vibrating screens are suitable for screening fine-particle materials, and have the characteristics of high screening accuracy and stable processing capacity. In a sand and gravel aggregate production line with an output of 800 tons per hour, multiple vibrating screens are usually configured to ensure that products of different particle sizes can be effectively separated.
Auxiliary equipment
In addition to the above main equipment, a sand and gravel aggregate production line with an output of 800 tons per hour also needs to be equipped with some auxiliary equipment to ensure the stable operation and efficient output of the production line. These auxiliary equipment include dust collector, water supply equipment, stone powder recovery equipment, etc.
1. Dust collector: The dust collector is responsible for collecting dust in the production line to reduce pollution to the environment. Commonly used dust collectors include bag dust collectors and cyclone dust collectors. Bag dust collectors have the characteristics of high dust removal efficiency and stable operation, and are suitable for collecting fine-grained dust. Cyclone dust collectors are suitable for collecting large-grained dust, and have the characteristics of simple structure and convenient maintenance.
2. Water supply equipment: The water supply equipment is responsible for providing the necessary water source for the production line to ensure the normal operation of the equipment and the quality of the product. Commonly used water supply equipment includes water pumps and water pipes.
3. Stone powder recovery equipment: The stone powder recovery equipment is responsible for recycling and utilizing the stone powder generated in the production line to reduce resource waste. Commonly used stone powder recovery equipment includes dewatering screens and sand washers.
Production line configuration case
The following is a configuration case of 800tph artificial sand making plant for reference:
1. Raw material: limestone
2. Equipment configuration:
Feeding system: 1 GZD1500*6000 vibrating feeder
Coarse crushing equipment: 1 PE-1200*1500 jaw crusher
Medium crushing equipment: 4 PFW1318 European version hydraulic impact crushers (or cone crushers)
Fine crushing equipment: VSI series sand making machine (select the model according to specific needs)
Screening system: 4 4YZS2460 circular vibrating screens (or linear vibrating screens)
Conveying system: several belt conveyors
Auxiliary equipment: bag dust collector, water pump, dewatering screen, etc.
3. Discharge particle size: 0-5mm, 5-10mm, 10-20mm, 20-40mm, etc. (adjusted according to specific needs)
4. Use of finished products: supply to surrounding commercial mixing stations and cement plants, etc.
Operation and maintenance of production lines
In order to ensure the stable operation and efficient output of the 800 tons per hour sand and gravel aggregate production line, the following work needs to be done:
1. Regular inspection and maintenance: Regularly inspect and maintain the equipment, timely discover and deal with potential faults, and ensure the normal operation of the equipment.
2. Operator training: Provide professional training for operators to improve their operating skills and maintenance awareness to ensure the safe and stable operation of the production line.
3. Equipment management: Establish a sound equipment management system, uniformly manage and dispatch equipment, and ensure the rational use and efficient operation of equipment.
4. Environmental protection measures: Strengthen the implementation of environmental protection measures, reduce the emission of pollutants such as dust and noise, and protect the surrounding environment.
In summary, the 800 tons per hour sand and gravel aggregate production line requires a series of professional equipment to work together, including feeding system, crushing system, conveying system, screening system and auxiliary equipment. Through reasonable configuration and optimized operation management, the stable operation and efficient output of the production line can be ensured, providing high-quality sand and gravel aggregate products for surrounding commercial mixing stations and cement plants.
Previous Article:No Information
Next Article: How to Produce High-quality Machine-made Sand?